Sectors
While legacy processes at best incrementally improve, PtFS is deployed where other options fail to meet projects exacting step-change requirements. Surface Generation’s ground-breaking technologies fix previously intractable problems in markets where compromise and / or performance, quality, traceability, energy efficiency and safety trades are simply non-negotiable.
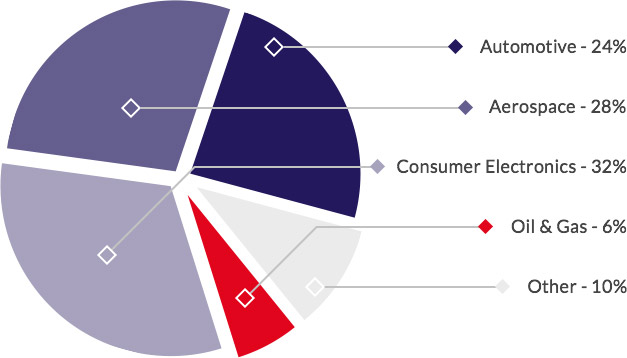